Comparing PCB Substrate Materials for Thermal Resistance and Performance
Comparing PCB Substrate Materials for Thermal Resistance and Performance
Printed circuit boards (PCBs) are an essential part of modern electronics, serving as the backbone for many devices from smartphones to medical equipment. The selection of the substrate material is a critical factor in PCB design, particularly when it comes to the PCB impedance, thermal resistance and overall performance. In this article, we will compare the thermal resistance and performance of three common PCB substrate materials: FR-4, aluminum, and ceramic, and provide recommendations for designers looking to optimize their PCB's thermal performance. We will also explore other substrate materials and provide additional examples of applications where these materials are commonly used.
Three common PCB substrate materials
FR-4 Substrate Material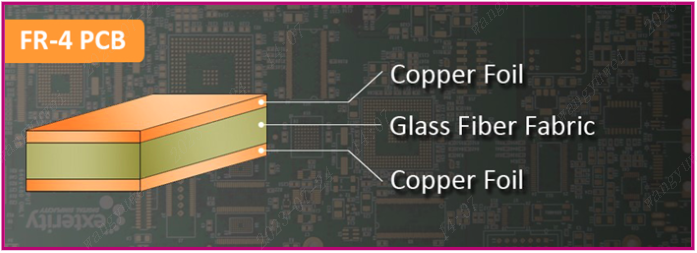
(Image credits: Jichangsheng Technology)
FR-4 is a widely used substrate material in PCB manufacturing. It is an epoxy-based laminate material that consists of woven glass fabric and a flame-resistant resin. FR-4 has good mechanical strength and excellent electrical insulation properties, making it a popular choice for many applications. However, it has a relatively low thermal conductivity, which can limit its ability to dissipate heat.
One way to improve the thermal performance of FR-4 is to use thicker copper layers and wider traces to increase the surface area for heat dissipation. Another option is to use thermal vias to provide a path for heat to escape from the component to the other side of the board. Furthermore, designers can use heatsinks to improve thermal management, although this can increase the cost of the board.
Aluminum Substrate Material
Aluminum is a metal-based substrate material that has excellent thermal conductivity and a high coefficient of thermal expansion. It is often used in high-power applications where heat dissipation is critical. Aluminum substrates can also be used as a base for heat sinks or other cooling solutions.
One specific example of an aluminum substrate is the insulated metal substrate (IMS), which consists of a thin layer of insulating material sandwiched between a layer of aluminum and a layer of copper. The aluminum layer provides excellent heat dissipation, while the copper layer provides good electrical conductivity.
Another application of aluminum substrate is in LED lighting. LEDs generate significant amounts of heat, and using an aluminum substrate can help dissipate that heat, increasing the lifespan and reliability of the LED.
Ceramic Substrate Material
Ceramic is another substrate material that is commonly used in high-power and high-frequency applications. Ceramic substrates have excellent thermal conductivity and mechanical strength and can operate at high temperatures. They are also resistant to corrosion and have good electrical properties.
One specific example of a ceramic substrate is the low-temperature co-fired ceramic (LTCC), which consists of multiple layers of ceramic material. The layers can be patterned with conductive traces using a screen printing process, allowing for the creation of complex circuits with integrated passive components.
Ceramic substrates are often used in applications that require high-frequency operation, such as microwave and radio frequency (RF) applications. They are also used in power electronics, such as DC-DC converters and motor drives.
Other Substrate Materials
Aside from FR-4, aluminum, and ceramic, there are other substrate materials that can be used in PCB manufacturing. For example, Rogers Corporation offers a wide range of high-performance materials for use in PCBs, including materials with high thermal conductivity, low dielectric loss, and low coefficient of thermal expansion. Another example is PTFE-based materials, which have excellent electrical properties and can operate at high temperatures, making them a popular choice for RF applications.
Polyimide is another substrate material that is commonly used in flexible PCBs. It has a high-temperature tolerance and can be used in applications where the PCB must bend or flex. Polyimide is often used in aerospace and defense applications, where the PCB must withstand extreme temperatures and harsh environments.
Recommendations for PCB Designers
When selecting a substrate material for a PCB, designers should consider the specific requirements of the application, as well as factors such as cost, availability, and ease of manufacturing. For high-power or high-temperature applications, materials such as aluminum or ceramic may be preferred due to their higher thermal conductivity. However, for lower power applications, FR-4 may be a more cost-effective and practical choice.
In addition to substrate material selection, designers should also consider other factors that can impact the thermal performance of the PCB, such as component placement, copper weight and thickness, and the use of thermal vias. Heat sinks and other cooling solutions can also be used to improve thermal management, although they can increase the cost of the board.
Examples of Materials and Applications
Other substrate materials and their applications include:
Teflon: This material has excellent dielectric properties and can operate at high temperatures. It is commonly used in microwave and RF applications.
Kapton: This material is a polyimide film that is often used in flexible circuits, such as those found in medical equipment and aerospace applications.
Metal core PCBs: These PCBs use a metal core, typically aluminum, as the substrate material. They are commonly used in high-power LED lighting and automotive applications.
Flexible PCBs: These PCBs use a flexible substrate material, often polyimide, thatallows them to bend and flex. They are commonly used in wearable technology, medical devices, and aerospace applications.
High-temperature FR-4: This material is a variant of FR-4 that is designed to operate at higher temperatures. It is commonly used in automotive and aerospace applications.
Ceramic-filled PTFE: This material combines the excellent electrical properties of PTFE with the high thermal conductivity of ceramic. It is commonly used in high-frequency and high-power applications.
JLCPCB PCB Fabrication and Assembly Service
JLCPCB's state-of-the-art manufacturing processes ensure that your PCBs are fabricated to the highest standards of quality and reliability. We also offer a user-friendly online ordering system that makes it easy to get a quote and place an order for your PCB project. With fast turnaround times, competitive pricing, and a commitment to customer satisfaction, JLCPCB is an excellent choice for designers looking for a reliable and high-quality PCB fabrication service.
Conclusion
In conclusion, the selection of substrate material is a critical factor in PCB design, particularly when it comes to thermal resistance and performance. Designers have a variety of substrate materials to choose from, each with their unique properties and benefits. FR-4, Aluminum, and ceramic are commonly used substrate materials, each with its strengths and weaknesses.
When selecting a substrate material, designers should consider the specific requirements of the application, as well as factors such as cost, availability, and ease of manufacturing. They should also consider other factors that can impact the thermal performance of the PCB, such as component placement, copper weight and thickness, and the use of thermal vias.
JLCPCB is a leading PCB fabrication and assembly service provider that offers a variety of substrate materials to choose from, including FR-4, Aluminium, Copper core, Rogers, as well as PTFE Teflon.
Recent Posts
• Best PCB Layout Design Guide For Prototyping
Mar 13, 2025
• PCB Antenna Design: Types, Principles, and Best Practices
Mar 15, 2025
• Converting a Hand-Drawn Circuit to a Professional Schematic
Mar 14, 2025
• Unlocking Top 5 Benefits of Flex PCBs in Electronics
Mar 10, 2025
• PCB File Formats
Mar 6, 2025